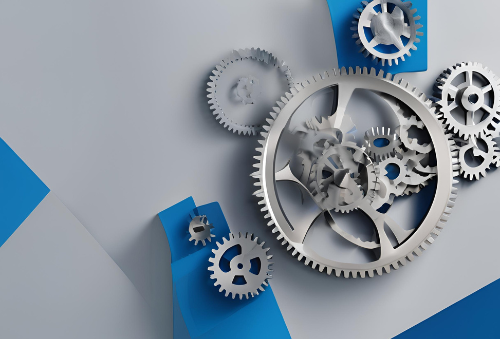
Atlas Copco
Products from U.S.A.
Compressor Valve
THE ZAHROOF STRAIGHTFLO VALVE
This revolutionary technology is patented around the world and offers significant improvements over conventional compressor valves. It is already widely used in Upstream, Midstream and Downstream Oil & Gas applications for reciprocating compressors.
The straight through flow design of the Zahroof valve results in a significant improvement in the performance and reliability of the compressor. There is low resistance to the flow of gas through the valve resulting in the improvement of valve efficiency. In most applications, the increased valve efficiency results in a reduction in power (along with reduction in emissions), or the ability to increase the throughput through the compressor at the same power (by reducing the clearance volume or increasing the compressor speed). This revolutionary technology is patented around the world and offers significant improvements over conventional compressor valves. It is already widely used in Upstream, Midstream and Downstream Oil & Gas applications for reciprocating compressors.
The straight through flow design of the Zahroof valve results in a significant improvement in the performance and reliability of the compressor. There is low resistance to the flow of gas through the valve resulting in the improvement of valve efficiency. In most applications, the increased valve efficiency results in a reduction in power (along with reduction in emissions), or the ability to increase the throughput through the compressor at the same power (by reducing the clearance volume or increasing the compressor speed).
Insight
The combination of the straight through flow design as well as the unique modular reed design, with no moving plastic components, results in a significant improvement in the reliability of the compressor. The StraightFlo™ valve’s unique straight through flow design performs very well in corrosive and/or dirty gas applications because valve tends to be self-cleaning as the flow carries contaminants through the valve (tolerance to liquids and solids), as compared to traditional valves where the gas flow directly impacts the sealing elements, often leading to valve failure and debris build up in the low-velocity regions of the flow passages.
More into It
The high natural frequency of the StraightFlo™ valve makes the valve more immune to failure due to pulsation and vibration issues. Moreover, field measurements show the valves produce on the order of 10 times less noise and vibration than traditional valves due to the absence of heavy plates, rings or poppets impacting directly on the seat and guard. The reduction in noise and vibration is very noticeable on the compressor deck.
From a design standpoint, one of the most innovative aspects of the StraightFlo™ valve is that all the sealing elements are contained in replaceable modules. As such, there is no wear and tear on the ZVI metal valve housings, a game-changing difference when compared to traditional compressor valves where the valve’s seat and guard suffer from wear and tear and require machining during valve repairs. With this differentiation, ZVI offers an industry-best 10-year warranty on its valve housings. In addition, since the modules are standardized in size, the same module can be used in various valve sizes, with larger valves holding more modules.
With replaceable modules, end-users no longer need to follow the traditional approach of stocking complete sets of spare valve assemblies to keep the compressor in operation while the worn set of valves is sent out for repair at a machine shop. With Straightflo™ valves, the modules can be easily replaced in the field, in about 10-15 minutes per valve, without any machining or skilled labor.
The modular design of the valves results in reduced inventory, especially when these valves are adopted across several compressors and several plants. Instead of stocking expensive, fully assembled valves, it is only necessary to stock modules that are not only significantly cheaper, but also have a much smaller footprint and mass. A compressor worth of modules can be stored in a couple of shoe boxes. Typically, 6 different module types are sufficient for all compressor operating conditions, irrespective of compressor brand or valve size.
Benefits
-
Reducing downtime and lost production due to the Zahroof StraightFloTM valve’s better life and reliability. Reed valves with no helical coil springs. Only moving parts are reeds with high resistance to fatigue.
Reducing service costs due to longer service intervals and the ability to service the valves onsite without any machining due to the modular design of the valves.
Reducing power costs due to improved efficiency and increasing revenue by increasing flow for the same power.
Reducing material costs as the valve housing never has to be replaced since Modules are held stationary between valve seat and guard, hence n wear of housing, (there is a 10- year warranty on the stainless-steel valve housing) and it is not necessary to buy a complete set of spares in the first instance.
Reducing emissions from better efficiency (lower power consumption) and from increased service intervals (reduced frequency of purging/flaring/venting compressor lines during service)
Reducing inventory by over 80%. 6-8 different module part numbers are all that is required to cover all operating conditions for all valves throughout the company irrespective of compressor brand and valve size.
FAMILY OF COMPRESSOR VALVES
StraightFlo™ valves have revolutionized gas compression operations worldwide by delivering unsurpassed reliability, savings, and sustainability benefits for reciprocating compressors.
ENGINEERED PERFORMANCE
All valves in the StraightFlo™ family are drop-in replacements for OEM valves and incorporate ZVl's patented Modular Reed Valve technology.
They provide superior performance across a full range of operating conditions, including speeds from 200 to 3,600+ rpm, pressure differentials across the valve to 4,350 psi (300 bar), service temperatures from -40° to 500°F (-40° to 260°C), and with all gases encountered in energy and industrial applications.
StraightFlo™ valves are optimized for each application in three key ways:
-
Valve seats and carriers are manufactured in two material types to provide the durability and cost-effectiveness required for their application.
StraightFlo™ Sf (Standard Edition) valves have 4140 steel alloy housings for long-lasting service with gases found in upstream and midstream oil and gas operations.
StraightFlo™ SS (Severe Service) valves have high chemical resistance from corrosive gases encountered in applications where required, including, but not limited to, refineries, petrochemical, chemical, and fertilizer applications.
Both valves are backed by a ten-year warranty on the valve housing.
-
Reed valve sealing modules are supplied in one of three material options based on requirements for chemical resistance, operating temperatures, and pressures.
-
ZVI engineers analyze operating conditions and customer requirements to optimize modules with the appropriate lift and stiffness to meet customer requirements for efficiency, throughput, and durability.
StraightFlo'" SS & StraightFlo'" SE
UNEQUALLED VALUE PROPOSITION
StraightFlo CONFIGURATIONS & SPECIALTY PRODUCTS
SINGLE DECK
-
Single layer for Modules
Integral Cage
-
Simplifies service and improves safety
Radial
-
High efficiency valve for transmission and pipeline applications
DOUBLE DECK
-
Highest effective flow area
Jack Bolt Eliminator
-
Simpler to torque, more reliable and secure
Unloaders
-
Reliable cylinder unloading plus StraightFloTM performance
Stacked
-
A second layer of Inset modules for Increased flow area A second layer of Inset modules for Increased flow area
Concentric
-
Compact space-saving design with suction and discharge in a single valve
Valve Protection Mesh (VPM)
-
Reduce damage from entrained solids and liquids
Learn more about the company: