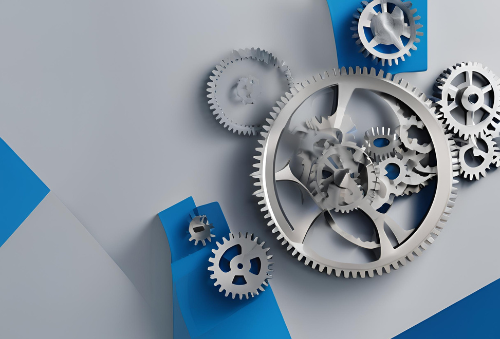
KAYDON
Kaydon Ring and Seal is the premier engineering and manufacturing source for rings and seals for demanding applications in the oil and gas, gas compression, and diesel locomotive industries, among many others.
Kaydon Seal Product
K-DGS Dry Gas Seal
-
At the heart of every K-DGS is the lift ramp geometry to generate and maintain lift force and clearance between the rotating and stationary seal faces. Kaydon's patented Tapered Lift Ramp geometry causes an increase in velocity of the seal gas as it moves through the ramp, sweeping contamination away from the sealing faces. (Other dry gas seal designs with constant depth geometry.
K-CBS Circumferential Barrier Seal
-
The K-CBS separation seal consists of segmented carbon rings that act as a wedge between the stationary housing and a hard-coated rotating shaft surface. The seals are buffered with gas at a pressure slightly higher than that of the cavities being separated. The seal rings are preloaded by a combination of radial garter springs and axial compression springs. Contact forces are minimized by pressure dams in both the side face and bore of each ring, which in turn minimizes wear and allows the seal rings to freely follow the movement of the shaft. The rings are designed with an initial overlapping clearance between segment ends. As the bore of the seals wear, the clearance decreases until the segment ends butt together. At this point, the ring is arch bound and continues to function as a clearance seal, providing the same reliable performance.
K-MRC Multi-ring Circumferential Gas Seal
-
The K-MRC is a standalone, dual purpose main shaft seal that prevents process leakage from escaping through the equipment bearings while also preventing bearing oil migration into the process. The K-MRC utilizes segmented carbon seal rings that act as a wedge between a stationary housing and a hard-coated rotating shaft surface. The seals are buffered with gas at pressure slightly higher than the regions being separated. The seal rings are preloaded by a combination of radial garter springs and axial compression springs. Contact forces are minimized by pressure dams in both the side faces and bore of each ring, which in turn minimize wear, and allows the seal rings to freely follow the movement of the shaft. The rings are designed with an initial overlapping clearance between segment ends. As the bore of the seals wear, the clearance decreases until the segment ends butt together. At this point, the ring is arch bound and continues to function as a clearance seal, providing the same reliable performance.
K-BOS Bushing Oil Seal
-
The Kaydon bushing oil seal (K-BOS) allows for tightly controlled leakage rates while maintaining a larger nominal clearance to the shaft. This is achieved by way of engineered pumping geometry in the bore of the process seal ring, which works with shaft rotation to generate a relative offset to seal oil pressure. This geometry is designed to provide optimal performance at normal operating speeds, while a short constant clearance section of the ring controls leakage rates during shutdown.

Kaydon provides a robust line of ring and seal products, from dry gas seals and mechanical seals to diesel and natural gas engine piston rings. Kaydon products solve specific application challenges and are enhanced by expert engineering to facilitate new installations, upgrades, troubleshooting, repair services, and support systems.
Gold-pated K-BOS for Corrosive Applications
Kaydon gold-plated bushing oil seals are ideal for hydrogen recycle and wet gas compressor applications where high concentrations of H2S or chlorides may form after rotor wash and attack traditional Babbitted bushings. Kaydon retrofits of gold-plated K-BOS seals have increased compressor run times from less than one year to 7+ years between seal overhauls.
K-MOS Mechanical Oil Seal
-
The K-MOS operates by using oil at 30-45 psi above process gas pressure to contain process gas inside the equipment body. The mechanical seal faces work to minimize the amount of oil flowing to the sour drain pots. Leakage is collected in drain pots where it is either treated and re-used or discarded. Sour oil leakage is normally less than five gallons per day and less than one gallon per day during standby. If you are experiencing higher levels of oil consumption with your current mechanical seals, contact us to discuss solutions.
Service & Support
Seals repaired by Kaydon are tested to required specifications and guaranteed to perform like new (or better). Kaydon has the engineering knowledge base, manufacturing capability, and test facilities to offer Kaydon certified, guaranteed seal repair for any make, any type, any model with quick turnaround and at a fraction of the cost of a new seal.
Kaydon Repair Work Scope
- Provide a detailed inspection report documenting condition of seals as received, causes for seal failure or performance issues, identifying components that will be reused or reconditioned and those that will be replaced
- Replace all O-rings, C-seals, springs and miscellaneous hardware items as required
- Check flatness and integrity of seal faces
o Rework critical sealing surfaces
o Reverse engineer or re-engineer parts requiring replacement
- Reassemble and test seals at operating speed and differential pressure specified
- Make recommendations for improved operation and reliability
- All seal repairs include Kaydon’s standard one year warranty
Partial List of Competitor Seal Repairs
- John Crane seals
- Flowserve
- Eagle-Burgmann
Learn more about the company: